Best Practices for Effective Tank Welding Inspection Processes
Best Practices for Effective Tank Welding Inspection Processes
Blog Article
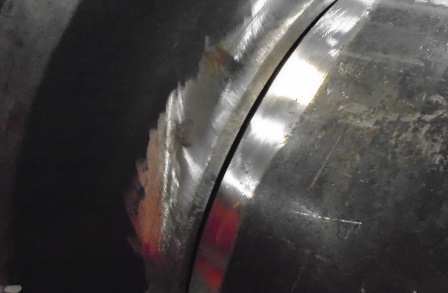
Understanding the Significance of Rigorous Storage Tank Welding Assessment Processes in Fighting Failures and Enhancing Lifespan
In the realm of commercial operations, the relevance of rigorous container welding evaluation procedures can not be overemphasized. By carrying out numerous inspection methods, organizations can spot problems early, therefore preventing costly consequences and extending the life of their storage space tanks.
Importance of Welding Assessments
Acknowledging the important duty of welding inspections in preserving architectural honesty, these procedures make certain that welds satisfy established requirements and specifications - Tank Welding Inspection. Effective welding assessments are extremely important in the building and construction and maintenance of storage tanks, as they directly influence the sturdiness and safety of the structures. By recognizing possible shortages, such as inappropriate techniques or material issues, inspections mitigate the danger of disastrous failures
Welding inspections include various methods, including aesthetic examinations, non-destructive testing (NDT), and assessments of welding treatments. Each approach serves to validate the top quality and conformity of welds with market guidelines, thereby guarding both personnel and environmental rate of interests. Additionally, routine inspections promote a society of responsibility and quality within the labor force, guaranteeing that all staff member comply with best methods.
Additionally, these evaluations add to the general lifecycle management of storage tanks by determining wear or destruction early while doing so. By resolving these problems proactively, organizations can extend the operational life expectancy of their possessions, eventually causing set you back financial savings and improved dependability. In recap, the relevance of welding examinations can not be overemphasized; they are vital for making sure safety and security, durability, and conformity in container construction and maintenance.
Common Reasons For Container Failures
Recognizing the common reasons of storage tank failures is vital for avoiding disastrous events and making certain the long life of storage systems. One widespread root cause of container failing is deterioration, which can considerably deteriorate the structural integrity of tanks gradually. Ecological variables, such as exposure to wetness, chemicals, and temperature variations, can accelerate this process.
Another crucial variable is inappropriate welding methods, which might lead to problems like fractures or incomplete joints. These problems can endanger the container's toughness and bring about leakages or tears. Additionally, inadequate upkeep techniques can result in unnoticed wear and tear, eventually raising the risk of failing.
Design defects, consisting of poor density or poor material selection, can additionally add to container susceptabilities. Operational factors, such as overfilling or direct exposure to extreme stress, can stress the container beyond its intended limits.
Secret Evaluation Methods
Effective inspection methods play a vital role in alleviating the threats connected with tank failings. A comprehensive approach to container welding inspection includes several essential methods, each developed to identify prospective issues and ensure architectural integrity.
Aesthetic evaluation remains the initial line of protection, permitting assessors to recognize surface area abnormalities such as splits, deterioration, or imbalance. This strategy is typically supplemented by non-destructive testing (NDT) approaches, which look at this site are essential for assessing weld quality without jeopardizing the container's stability.

Moreover, magnetic particle testing (MPT) and color penetrant testing (DPT) are effective for spotting surface issues in ferromagnetic materials and non-porous surface areas, specifically. Each method has its staminas and limitations; as a result, a mix of methods is often employed to attain detailed evaluation outcomes.
Advantages of Rigorous Examinations
While the instant expenses of extensive assessments may seem daunting, the long-term advantages significantly exceed these preliminary find more investments. Applying thorough assessment processes not only enhances the integrity and security of container structures however additionally minimizes the danger of disastrous failures that can cause substantial economic losses and environmental injury.
Rigorous assessments help determine prospective concerns early in the welding process, allowing for timely restorative actions that avoid costly repairs or substitutes down the line. This aggressive technique promotes a society of quality control, where adherence to best practices comes to be instilled in functional treatments. Moreover, routine inspections add to boosted asset durability, as they ensure that tanks remain in optimal condition throughout their life-span.
Furthermore, the documentation generated from these evaluations works as a valuable resource for maintenance preparation and efficiency examinations. This data-driven technique can additionally improve functional performance, resulting in minimized downtime and enhanced performance. Inevitably, strenuous examinations not just guard the structural stability of containers yet likewise supply considerable financial advantages, enhancing the concept that spending in top quality guarantee is a smart decision for any type of organization involved in storage tank operations.
Regulative Standards and Conformity
Governing criteria and compliance are important elements of tank welding assessment procedures, as they establish the structure for ensuring security and high quality in procedures. Conformity with these standards not only reduces risks but likewise boosts the overall integrity of bonded frameworks. Various companies, including the American Culture of Mechanical Designers (ASME) and the American Oil Institute (API), give standards that determine appropriate practices for welding, inspection, and screening.
These requirements mandate making use of certified employees, the application of rigorous assessment procedures, and adherence to certain welding procedures. By aligning with governing requirements, companies can make sure that their storage tanks fulfill the necessary security and efficiency criteria, thus decreasing the likelihood of tragic failures that can lead to considerable economic this contact form losses and environmental damage.

Furthermore, regulative compliance fosters a society of accountability and continuous renovation within the welding and fabrication markets (Tank Welding Inspection). Regular audits and inspections guarantee that practices continue to be lined up with evolving standards, thus promoting long-term dependability and functional performance. Eventually, adherence to regulative criteria not just shields assets yet additionally boosts the lifespan of welded storage tanks, guaranteeing they serve their designated purpose successfully with time
Final Thought
In conclusion, rigorous storage tank welding evaluation procedures play an important duty in preventing failures and extending the life-span of storage frameworks. By identifying possible deficiencies through various assessment strategies, companies can alleviate threats connected with tank stability.
Report this page